«МЫ ХОТИМ САМИ ДЕЛАТЬ ОКОННЫЕ ПРОФИЛИ! ЧТО НАМ НУЖНО ДЛЯ ЭТОГО ЗНАТЬ?»
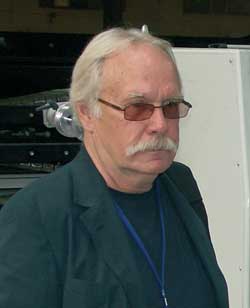
Сразу хотелось бы подчеркнуть, что многочисленные цифры, которые здесь приводятся, разумеется не являются, так сказать, сиюминутными, хотя в основном и близки к реальным; такая задача, впрочем, и не ставилась, поскольку наша цель иная – показать, чего нельзя упустить при организации производства оконных профилей и расчете его рентабельности.
Прежде всего, уважаемый читатель, нужно выбрать наиболее оптимальный для Вас ассортимент профилей. Для начинающего производителя оконных профилей следует исходить из необходимости выпуска минимального их набора, обеспечивающего «самодостаточность», т. е. возможность производить 70 – 80% наиболее часто заказываемых окон и дверей из собственных профилей, прибегая к закупкам дополнительных профилей и доборников лишь в редких случаях (арки, эркеры, остекление балконов и т. д.). Для этого нужно знать, к какой из ходовых оконных систем Ваши профили должны подходить. Надо также определиться с количеством камер, толщиной стенки, числом и типом уплотнений, дизайном (например, мягкий или угловатый контур, плоскосмещенная или плоскосовмещенная створка), оптимальным соотношением метража рамы, створки, импоста, штапика и т. д.
К базовым профилям мы могли бы отнести в первую очередь следующие:
- оконная рама
- оконная створка
- импост рамы
- импост створки
- дверная створка
- штапик для стеклопакета 24 мм
- штапик для стеклопакета 32 мм
- штульп
Необходимое оборудование
Набор высококачественных и высокопроизводительных экструзионных инструментов известных европейских фирм (фильеры, сухие и влажные калибраторы), являющихся «сердцевиной» экструзионного процесса, для производства такого ассортимента профилей стоит в общей сложности порядка 450 – 500 тыс. ЕВРО (здесь и далее отпускные цены завода).
Для оптимальной загруженности экструзионного производства и, соответственно, как можно более высокой его рентабельности эти инструменты нужно использовать минимум на двух линиях (одна для главных профилей с большей производительностью 200 – 250 кг/ч, другая для вспомогательных профилей – 100 – 120 кг/ч). Две такие полностью укомплектованные линии могут быть приобретены в сумме за 400 – 450 тыс. ЕВРО.
Для полной комплектации нужно также периферийное оборудование: смеситель, холодильная установка, 2 содозатора для загрузки дробленого профиля (регенерата), мельница для регенерата, ламинационная установка, установка для ультразвуковой очистки инструмента, что также может быть поставлено в комплекте оборудования «под ключ» по суммарной цене около 300 тыс. ЕВРО.
Итого, капитальные затраты (стоимость оборудования) составят 1200 – 1250 тысяч ЕВРО
В последние годы у китайских, корейских и турецких поставщиков все это оборудование можно купить заметно дешевле, а зачастую и с ненамного худшим, а то и с равным качеством.
Некоторые фирмы готовы поставлять это оборудование с частичной рассрочкой платежей при условии предоставления удовлетворительных гарантий. Речь может идти о рассрочке до 3 лет на 50 – 60% стоимости оборудования под годовой процент 5 – 7%. Возможны и значительные скидки, которые зависят и от состава оборудования, и от условий платежа. Т. е. возможен вариант оплаты авансом всего около 200 тыс. ЕВРО и еще 300 тыс. ЕВРО до отгрузки оборудования, а если удастся выторговать скидку, то и того меньше. Остальная сумма – месячными платежами в течение 3 лет.
Сюда нужно также добавить стоимость транспортировки и растаможки оборудования, включая НДС, что составит примерно 25% от его стоимости, т. е. около 350 тыс. ЕВРО. Есть, правда, способы минимизировать эти расходы до 100 – 150 тыс. ЕВРО, что может быть темой отдельного обсуждения.
Таким образом, общая стоимость поставки оборудования с учетом обслуживания кредита составит порядка 1,4 млн. ЕВРО
Необходимо при этом отметить, что ряд фирм берут на себя разработку системы оконных профилей и рецептуры сырья, обучение специалистов, доводку инструментов на своем заводе и у покупателя, пусконаладку оборудования, обеспечение гарантийного обслуживания и последующий сервис с поставкой необходимых запчастей, и это уже как бы включено в указанную цену. Но это нужно четко оговаривать еще на стадии подготовки контракта.
Производственные площади
Мы исходим из того, что цех для установки этого оборудования, или, как говорят, «коробка», у Вас уже имеется. В его полу необходимо будет проделать каналы для прокладки коммуникаций к экструзионному оборудованию для подвода воды, воздуха и электроэнергии, а также сделать 2 емкости для воды по 30 куб. м ниже уровня пола. В первом приближении на эти строительные работы может потребоваться 50 – 70 тыс. ЕВРО.
Необходимо иметь также трансформаторную подстанцию (установленная мощность оборудования около 450 кВт), компрессор (на 60 – 70 куб. м/ч сжатого воздуха), водоподготовку (на 60 куб. м/ч с очистными фильтрами). В цеху желательно иметь кран-балку грузоподъемностью не менее 5-6 тонн.
На две линии требуется площадь порядка 30–35 х 7–8 метров. Необходимо также иметь площадь для смесителя, мельницы, участка ухода за экструзионными инструментами, ламинирования профилей с вытяжкой (при использовании варианта с растворителем), складирования сырья и готовой продукции, лаборатории контроля входящего сырья и готовой продукции, офиса. В общей сложности потребная площадь составит не менее 550 – 600 м2 (30х20 м). При этом следует учесть, что никто на двух линиях не останавливается, т. е. цех желательно иметь с запасом как минимум еще на пару линий.
Итак, ввоз оборудования и минимальный объем подготовительных работ в цеху потребует около 1,5 – 1,6 млн. ЕВРО
Текущие затраты
Далее нужно посчитать требуемые текущие затраты, а именно: стоимость сырья, материалов, энергоносителей, логистики, труда (зарплату), а также амортизацию.
Будем исходить из того, что стоимость так называемой сухой смеси (dry blend) составляет около 1,3 ЕВРО за кг (данная цена взята только как пример для расчета!). Она складывается из стоимости ПВХ (около 0,9 ЕВРО/кг), на который приходится в зависимости от рецептуры в среднем 80% веса этой смеси, и аддитивов (порядка 2,5 ЕВРО/кг). Более надежный вариант, когда аддитивы закупаются в уже расфасованном виде (all-in-compound), соответствующем определенному количеству ПВХ. Т. е. в смеситель загружается, например, 100 кг ПВХ марки С 7059 М в мешках по 25 кг и на это количество ПВХ в смеситель закладывается пластиковый пакет с уже заранее расфасованными фирмой-поставщиком аддитивами даже без необходимости его разрывать (примерно 22-23 кг). Можно, конечно, развешивать аддитивы и самому перед загрузкой, но здесь есть риск допустить ошибку, а значит получить плохое качество смеси и, соответственно, профиля. Промежуточный вариант – это когда приобретается стабилизатор в пакете one-pack у одного из ведущих европейских поставщиков, а мел, двуокись титана и модификатор у других поставщиков, в том числе отечественных.
На указанном оборудовании при трехсменной работе и общем времени работы за год порядка 6 тыс. часов можно произвести 2 тыс. тонн профиля (при налаженном производстве и сбыте эти показатели могут быть повышены на 30 – 40%). В первом случае стоимость сырья составит около 2,6 млн. ЕВРО.
Если исходить из того, что одна треть профилей будет ламинироваться (скажем, рама, створка, импост с двух сторон, штапик с одной стороны), то расходы на ламинирующую пленку и клей составят в сумме около 32 тыс. ЕВРО в год (при цене пленки 0,5 ЕВРО/кв. м и клея 0,4-0,5 ЕВРО/кв. м).
Годовая стоимость потребляемой электроэнергии для установленных мощностей составит около 40 тыс. ЕВРО.
Зарплата из расчета на 5-6 человек – также порядка 40 тыс. ЕВРО.
Амортизацию оцениваем в среднем в 10% в год, т. е. около 100 тыс. ЕВРО.
Общие годовые затраты на экструзию указанной системы профилей составят 2,8 млн. ЕВРО.
За год на указанных линиях можно произвести около 800 тыс. «комплектных» метров профиля (1 м рамы + 1 м створки + 1 м штапика), если исходить из того, что погонный метр рамы весит около 1,1-1,2 кг, створки – 1,2-1,3 кг, штапика на 24 мм – 0,20 кг. Примем, что прейскурантная цена «комплектного» метра белого профиля составляет порядка 200 – 250 руб., а ламинированного – 400 рублей (рама и створка с двух сторон, штапик – с одной). При принятом соотношении белого и ламинированного профиля 2/3 и 1/3 общая годовая стоимость проданного профиля может составить 5,8 млн. ЕВРО. Учитывая, однако, что примерно 1/3-1/4 произведенного профиля зачастую идет на собственное оконное производство, т. е. по себестоимости, а остальное будет продаваться с определенными оптовыми скидками и испытывать сезонные спады, реальный годовой объем продаж можно определить в 4-5 млн. ЕВРО.
Расходы на организацию сбыта, складское хозяйство и транспорт потребуют примерно 50 тыс. ЕВРО в год.
Разница между годовой стоимостью продаж и годовыми текущими затратами составит в этом случае около 1 – 2 млн. ЕВРО, т. е. рентабельность будет на уровне порядка 35 – 50%.
Подводя итог, можно сказать, что затраты на ввоз и установку указанного оборудования при его нормальной загрузке и эксплуатации окупятся примерно за 2 года.
При достаточно бесперебойном производстве, хорошо налаженном сбыте на рынке, а также при меньших инвестиционных и производственных затратах данные по рентабельности могут быть и заметно выше.
О. Юрыгин, директор московского представительства DAC International/Houston, Moscow, Amsterdam