Интересное, перспективное и прибыльное в ламинировании профилей из ПВХ, алюминия и МДФ
Также многие современные дизайнеры концептуально разрабатывают проекты интерьеров квартир и домов, в которых все: от мебели, стен, окон, дверей, подоконников и до плинтусов и порогов «выстроено» в одной цветовой палитре и фактуре.
Среди преимуществ ламинированных декоративной ПВХ-пленкой профилей можно выделить следующие:
- высокая защищенность от механических повреждений (царапин, сколов)
- абсолютная устойчивость к погодным условиям (пленка не выцветает на солнце, нечувствительна к осадкам, легко выдерживает перепады температуры от -80°С до +130°С)
- гарантированная долговечность (до 20 лет)
- эстетичный внешний вид
- стойкость к любым моющим средствам, в том числе кислотосодержащим
Оборудование для ламинации
Ламинирующие станки различаются в зависимости от того, какие используются системы нанесения клеев:
- с помощью ракеля: двухкомпонентный холодный клей на основе растворителя
- с помощью дюзы: термопластичный клей-расплав (иначе говоря, полиуретановый клей / горячий клей / хотмелт, EVA или полиолефин)
- с помощью вальцов: ЭВА и полиолефин
Возможно совмещение на одном станке двух систем клеенанесения, но станок для этого должен быть удлинен.
Кратко о видах нанесения данных клеев
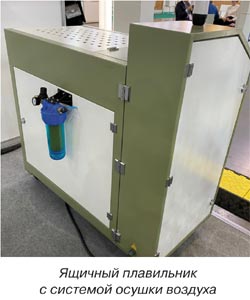
Двухкомпонентный холодный клей (на основе растворителя) наносится на ламинационную пленку (через ракель), которая затем протягивается через нагревательный туннель, где растворитель, находящийся в составе клея, ускоренно испаряется. Расход клея в данной технологии в диапазоне 80 – 120 граммов на 1 м².
По второй технологии клей-расплав в брикетах разогревается в специальном плавильнике (ящичном или бочковом) и через нагревательный шланг подается в дюзу. Дюза является своеобразной «кисточкой», которая наносит расплавленный горячий клей на пленку строго на ширину выставленного размера и толщину клея (выставляется из учета расхода 40 – 60 граммов на 1 квадратный метр, в зависимости от особенностей ламинационного материала, его структуры и фактурности, от химического состава и характеристик клея и т. д.).
Полиуретановый клей-расплав не содержит растворителей; в процессе его остывания происходит реакция образования полимерной сетки, в результате чего достигается значительное улучшение свойств клеевого соединения (прочности, влаго- и паростойкости).
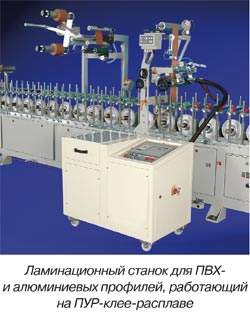
И в том и в другом случае, независимо от типа клея, осуществляется подготовительная обработка поверхности ПВХ- и алюминиевого профилей (поверхность профиля необходимо обработать праймером).
Для работы с полиуретановым клеем (клеем-расплавом, хотмелтом, горячим клеем) используют плавильники. Плавильники могут быть разных видов: ящичные (на 18 – 20, 50 и 100 кг/литров загрузки клея) и бочковые (на 18 – 20 и 200 кг загрузки клея). В некоторых ящичных плавильниках предусмотрена возможность работы не только с ПУР-клеем-расплавом, но и с полиолефином и EVA-клеями.
В процессе ламинирования происходит постоянный контроль следующих параметров: оптимального расположения пленки относительно профиля, качества ламинируемой поверхности профиля и качества нанесения и высыхания праймера (функция грунта) на поверхности профиля, скорости ламинации и степени прижима ламинационных роликов.
Если же речь идет о приклеивании ПВХ-пленки, листового или рулонного шпона, или меламинового ламинирующего материала к МДФ-профилю, то здесь предпочтение следует отдавать станкам, работающим на ПУР-клеях-расплавах, EVA-клее или полиолефине.
В настоящее время в производственной палитре оборудования для ламинирования/каширования профилей имеются станки, позволяющие наносить пленку, бумагу, меламин (как рулонный, так и листовой) и шпон шириной от 10 до 1400 мм со скоростью до 40 – 80 м/мин.
С целью расширения технологических возможностей производимого и реализуемого оборудования были разработаны ламинирующие станки с использованием в них двух систем нанесения клея:
- для рынка ПВХ-профилей и алюминия: двухкомпонентного холодного на основе растворителя + ПУР-клея-расплава
- для рынка МДФ-профилей: ПУР-клея + листового шпона с помощью EVA-клеев и полиолефина (вальцовая система нанесения клея)
Это позволяет существенно экономить рабочее пространство и финансовые вложения, а также расширяет ламинационные возможности, например, позволяет осуществлять заказы «на сторону» с применением различных материалов (ограничение составляет только ширина пленки), разнообразной геометрии профилей.
Для оптимальной и существенной экономии производственной площадки и времени ламинации своим клиентам мы предлагаем станок для одновременного двухстороннего ламинирования ПВХ-пленкой оконного, строительного и мебельного профилей. В данных станках, работающих на клее-расплаве, ламинация профилей осуществляется с подачей пленки сверху или снизу. Возможная скорость ламинирования профилей на таких станках – до 40 м/мин.
Данные установки уже успешно работают в Германии, Турции и в Арабских Эмиратах.
Вопрос количества (в граммах на 1 кв. метр) наносимых клея и праймера играет немаловажную роль как в экономическом, так и в технологическом смысле. Отсутствие контроля регулировки и настройки этих сырьевых материалов негативно сказывается на рентабельности самого готового изделия «на выходе». Любой производственник сможет легко подсчитать, сколько денег он сэкономит в месяц, если вместо 80 – 120 г/м² двухкомпонентного холодного клея, наносимых фактически «на глаз» (при работе с двухкомпонентным холодным клеем на основе растворителя), он будет наносить 40 – 60 граммов на 1 квадратный метр при работе с ПУР-клеями.
Праймер по технологии должен расходоваться 15 – 20 г/м², а не 60 – 100 г/м², как происходит на многих отечественных предприятиях в России. Для контроля расхода праймера нашей компанией была разработана система автоматического нанесения и контроля уровня праймера, позволяющая существенно экономить на затратах по его использованию.
В последнее время вопросам экологии и сохранения окружающей среды уделяется повышенное внимание. Не остаются в стороне многие отрасли промышленности, в частности, ламинационное производство: многие предприятия в Европе стремятся перейти от технологии применения клеев с содержанием растворителей на системы, свободные от этих испаряющихся в атмосферу веществ, а именно на полиуретановые клеи-расплавы. Такое стремление обосновано еще и тем, что данный вид клея прошел сертификацию в специализированном институте по контролю и выдаче сертификатов Suddeutsches Kunststoffzentrum (Центр по пластмассовым материалам) в немецком городе Вюрцбурге.
Наиболее экологически ответственные компании-производители оконных и дверных ПВХ-профилей выставляют требование: ламинировать их профили только с помощью ПУР-клеев-расплавов, которые нетоксичны, не требуют спецразрешений для перевозки и имеют гораздо больший срок хранения, чем двухкомпонентный клей холодного нанесения на основе растворителя. Ну а кроме того, при работе с ПУР-клеями-расплавами есть множество технологических преимуществ, которые отражаются на качестве конечного заламинированного продукта.
В связи с вышесказанным, а также с тем, что стоимость двухкомпонентного холодного клея за последние десять лет практически сравнялась со стоимостью ПУР-клеев, многие российские заводы также переходят на ПУР-системы, позволяющие в разы экономить на расходе клея (расход двухкомпонентного холодного клея на основе растворителя 80 – 140 г/м2, а расход ПУР-клея-расплава 40 – 60 г/м2).
В данной ситуации наша компания может предложить не только ламинационные станки, работающие на ПУР-клеях-расплавах, но и как один из вариантов: переоборудование имеющегося на производстве ламинационного станка, работающего на двухкомпонентном холодном клее на основе растворителя, под ПУР-клеи-расплавы. Мы являемся одними из немногих, кто не просто собирает ламинационные станки, но и производит собственные плавильники и дюзы.
Итак, чтобы перевести (модернизировать) ламинационный станок на ПУР-клеи-расплавы (иными словами, горячие клеи), потребуется ламинационный станок (работающая станина с транспортными колесами, прижимными роликами). Станок может быть любого производства, будь то Испания, Германия, Турция, Китай. Самый старый станок, который нам довелось перевести на ПУР-клей-расплав, был 1978 года производства, выпущен компанией FRIZ. При проведении модернизационных работ на станину станка устанавливается ПУР-станция (состоящая из пневматического вала размотки с электропневматическим тормозом, оптической электронной системы, дюзы, первого прижимного вала) с плавильником (мощность и объем плавильника подбирается в зависимости от профилей, объемов клиента и желаемой скорости ламинирования). Производятся электромонтажные работы со шкафом управления станка. Для этого желательно иметь электросхемы, впрочем, их отсутствие некритично, оно просто немного затормозит электромонтажные работы. Заключающим этапом модернизации является синхронизация работы станка с ПУР-плавильной станцией. Ниже приведены фотографии станков с установленными на них нашими ПУР-плавильными станциями.
Только за последние 15 лет наша компания провела свыше 400 аналогичных модернизаций на станках разной ширины (от 300 до 1300 мм). Еще раз хотим отметить, что при смене систем клеенанесения следует учитывать, что ПУР-система, которая будет устанавливаться на станок, это не просто «дюза + шланг + плавильник», это целая установка, включающая в себя размоточный пневматический вал (один либо два, все зависит от технических задач и того, где будет эксплуатироваться ламинационный станок: в составе экструзионной линии или нет), оптическую систему, нагревательные элементы, плавильник и все необходимые опционы к нему, а также то, что меняются электрические соединения в шкафу управления, производится синхронизация ПУР-системы с работой ламинационной установки и иногда экструзионной линии (если станок используется в составе экструзионной линии).
Многие производители оборудования уверяют, что они могут предложить ламинирующие станки, работающие со скоростью до 100 м/мин. Однако следует учесть, что качество ламинирования во многом определяется технологическими требованиями (например, наносимый праймер должен успеть высохнуть до того, как пленка с клеем прикатается к профилю и т. д.), качеством, эластичностью и фактурностью ламинационного материала, шириной и геометрией профиля, а также человеческим фактором (при скорости 80 – 100 м/мин обслуживающий персонал будет просто не в силах отследить «сохраняемость» параметров процесса, а значит, и качество ламинации от этого будет страдать).
Более подробно о ламинационных тонкостях и себестоимости ламинационного процесса можно узнать, позвонив в офис компании «ТПК «Экстру-Тех» или прислав нам заявку с указанием того, какие профили планируется ламинировать и какими материалами.
Наталья Сологуб, генеральный директор ООО «ТПК «Экстру-Тех»